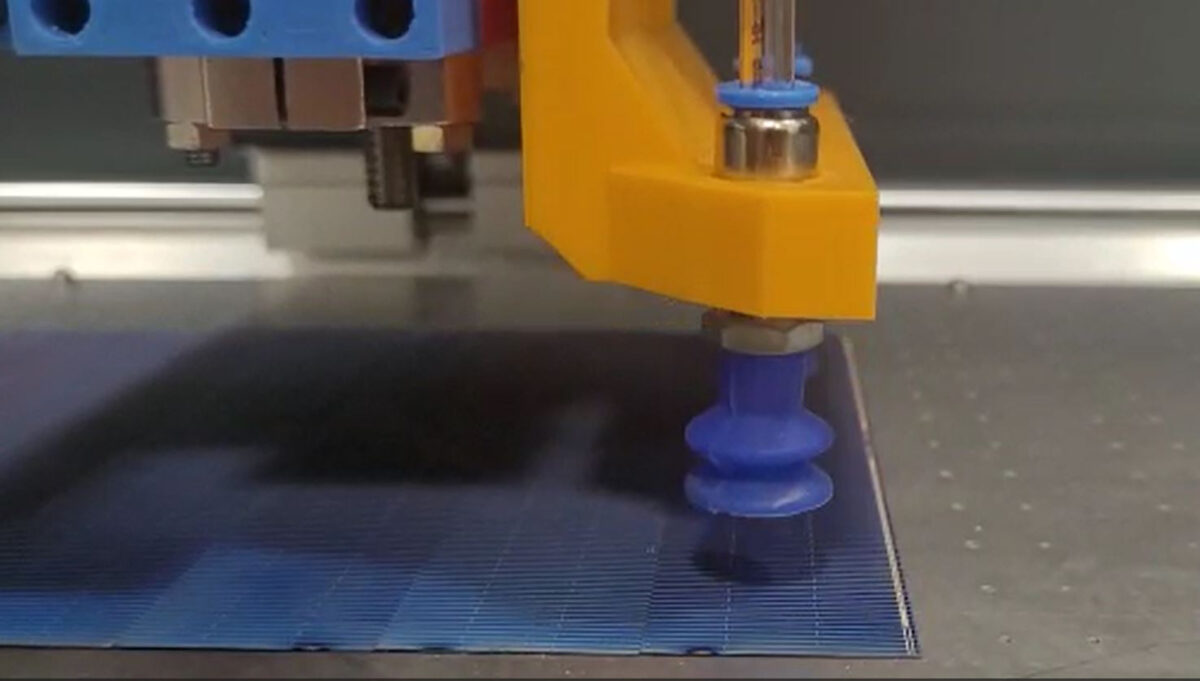
Scientists in Turkey have conceived new solar module electrically conductive adhesives based on silver microflakes and optimized polymeric additives. The proposed adhesives were found to increase electrical conductivity, adhesion strength, and reliability under real-world operating conditions.
Researchers at the Middle East Technical University (METU) in Turkey have developed water-based electrically conductive adhesives (ECAs) designed specifically for shingled PERC-type solar cells.
Shingled panels feature a busbar-free structure in which only a small proportion of cells are not exposed to sunlight. The cells are bonded with electrically conductive adhesive to form a shingled high-density string and the resulting strips are connected. The reduced number of busbars reduces shadowing losses.
“Unlike conventional solvent-based adhesives that emit volatile organic compounds (VOCs), the newly formulated adhesive is entirely water-based, offering a green and safe alternative for photovoltaic manufacturing,” the research’s lead author, Husnu Emrah Unalan, told pv magazine. “By using silver micro-flakes, biodegradable additives, and optimized surfactants, the formulation achieved volume resistivity of 22 μΩ/cm at a film thickness of 25 μm, an adhesive yield stress of 4.8 MPa, and a 0.4% absolute increase in power conversion efficiency compared to a commercial reference adhesive.”
In the paper “Waterbased electrically conductive adhesive for PERC-type shingled solar cells,” published in Solar Energy Materials and Solar Cells, the research team described the novel ECA as a water-based system incorporating Ag micro-flakes as the conductive filler, with the primary components being an unspecified environmentally friendly binder system, dispersants, and rheology modifiers.
The binder was chosen due to its organic, water-soluble, biodegradable, and environmentally friendly properties, the academics said, without providing further details.
“The specific formulation of the electrically conductive ink used in this study is currently the subject of a pending patent application, and detailed composition information cannot be disclosed at this time,” they added. “All other materials and processing parameters will be described to the extent necessary to ensure reproducibility of the methods used in this study, while proprietary details remain protected.”
The scientists validated the performance of the ECA through full outdoor testing at the METU-GÜNAM photovoltaic module outdoor test field in Ankara, Turkey, with real-world tests confirming the adhesive’s electrical and mechanical reliability over time.
They applied the ECAs via direct ink writing (DIW) with a 27-gauge nozzle with an inner diameter of 0.21 mm to carry out deposition and control adhesive distribution. For two interconnected strips, they used 0.1 g of ECA, while for a full set of 15 pairs of strips, the total ECA consumption was 16 g.
The validation process showed that the ECA offered homogeneity, high packing density, and the desired rheological properties for PV applications. It was also found to provide high-strength adhesion without forming porosity and agglomeration in microstructure, which the researchers said is key to achieving good performance in solar cell interconnections.
“This development represents an important step toward sustainable solar panel assembly and holds promise for integration in flexible electronics, wearable devices, and green electronic manufacturing lines. Commercialization processes of the conductive adhesive continue at spin-off company, Nanonovatif Material Technologies,” Emrah Unalan concluded.
This content is protected by copyright and may not be reused. If you want to cooperate with us and would like to reuse some of our content, please contact: editors@pv-magazine.com.
Source link